By 2050, the world should have installed at least 60 TW of solar and more than 200 GW/1,200 GWh of energy storage, if current projections are to be realized, thus meeting around 70% of the world’s total primary energy demand. By then, the electrification of industries like transport and heating should also have evolved, helping us to significantly combat our fossil fuel addiction.
The work toward ambitious renewable energy targets is well underway. However, it is imperative that it goes in the right direction – not only to develop as sustainably as possible but also to address the critical supply chain issues facing us and upcoming new legislation, like the environmental, social, and governance (ESG) rules that focus on scope 1, 2, and 3 emissions. This means starting from the very beginning with product design and materials.
In particular, scope 3 emissions – all indirect upstream and downstream emissions, i.e., from supply chains – are coming increasingly to the fore. According to the United Nations Global Compact, they account for over 70% of the carbon footprint of most businesses. This means, there is potential to make significant strides in sustainability, and material and cost reductions.
More means more
In a study by researchers from the Institute for Social Ecology at the University of Natural Resources and Life Sciences Vienna, published in the Journal of Cleaner Production and titled “Material requirements of global electricity sector pathways to 2050 and associated greenhouse gas emissions,” it was discovered that while renewable energy power systems can reduce greenhouse gases (GHGs), they require more raw materials to build than their fossil fuel counterparts.
The research team from the BOKU Institute for Social Ecology as part of the EU project MatStocks, calculated the material requirements and associated GHG emissions of in the 281 scenarios in the electricity sector up to 2050.
The team found that “the material requirement in scenarios that match the 1.5 C target is significantly higher than in scenarios that exceed a global temperature increase of 2 C. This is because more material has to be invested in the expansion of photovoltaics, wind power and other renewable technologies per amount of electricity generated than with fossil or nuclear energy.”
The authors continue, “Material stocks in 2050 differ by up to 30% for copper, 100% for concrete, 150% for iron/steel and 260% for aluminum, even excluding the particularly material-intensive scenarios that limit global warming to below 1.5 C. Although power plants account for most of the material requirements, grid expansion and reinforcement, which are necessary to accommodate a large part of the volatile power generation and to ensure universal access to electricity, also cause significant material requirements.”
These industries are not only key to renewables but also sectors like transportation and infrastructure. Overall, materials like iron/steel, aluminum, copper, and cement account for one seventh of annual GHG emissions globally. By taking a sustainable approach now, the solar and energy storage industries can benefit from and/or lead a new approach to how they are produced.
In the PV industry, for example, steel is often the preferred material for mounting systems – precisely because of its low carbon footprint and high recyclability when compared to aluminum. However, steel production is still one of the most energy-consuming and CO2 emitting industrial activities in the world. Its manufacture can also contributes to dangerous levels of water and air pollution.
There are moves in the industry to create a circular steel economy, with actors like ArcelorMittal, a leading supplier of steel and a major player in the solar industry which plans to create a circular steel economy. To achieve this, it has launched its XCarb program, and has already earmarked $10 billion to reduce its European CO2 emissions intensity by 35% by 2030 and be carbon-neutral by 2050. The program encompasses circular carbon and carbon storage projects, and clean power generation. It further aims to use hydrogen instead of natural gas in the direct reduction of iron ore.
Sharp focus
Material use is coming into sharp focus in the cell and module space too. As PV industry veteran Pierre Verlinden said when kicking off the first sustainability session at the 2020 pv magazine Roundtables Europe event, if solar is to scale to the terawatt level required to achieve a zero-emission global economy, it is incumbent on the industry to provide for product end-of-life reuse and to meet looming material challenges. “As of today, only a small part of this whole [solar] recycling process is actually used and we recycle very few materials from the entire PV system,” said Verlinden. “We still need to do much more than that.”
Recycling is important (see UP Initiative Q4 2020: PV Module Recycling) and in the last year alone, there have been many announcements highlighting improvements in the way modules, for example, are dealt with at end of life. However, this alone will not be enough to address the material shortages we face going forward.
At this year’s Roundtables Europe event, Verlinden’s point was reiterated by Alison Lennon, chief scientist at Sundrive Solar and adjunct professor at the University of New South Wales. “It is a very interesting time in PV manufacturing. People are realizing that PV is going to play a major role in decarbonization, and most manufacturers are critically looking at their supply chains to make sure they can sustainably produce materials,” she said.
“With the cells, the material that’s come into focus has been the use of silver. Most modules use silver for their cell metallization. With the current PERC [passivated emitter rear contact] technology, they use around 15 tons per GW of production. If you were to scale that to produce 1 TW, then you’re going to use up more than 50% of the world’s 2019 silver production.”
Through her work, Lennon and colleagues are focusing on developing high efficiency, sustainable solar cell technologies. Their research suggests that silicon heterojunction solar cells offer high efficiency and a good path to tandems while the silver can be replaced with copper pastes and plating. There are still challenges to overcome, she said, but the problem is not unsolvable.
“If you move onto modules, they use a lot of glass and aluminum, and you need to think about those materials. Although aluminum is not in short supply, if you produce it by primary production – and we will need to do this because there are not enough modules to be recycled – the emissions that will be generated are quite substantial. It’s going to be critical for the aluminum industry to decarbonize quickly,” she said. “Like silver, it’s not insurmountable, but it does need the industry to consider decarbonizing very quickly so that we can produce modules with low emissions.”
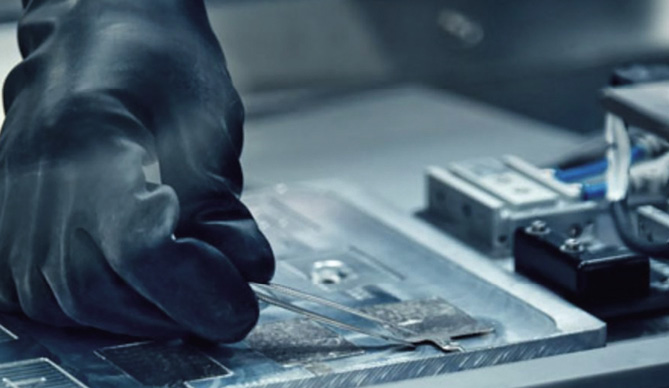
Image: Deakin University
Unrealistic aims
Batteries are indispensable for e-mobility and the energy transition; however, the technology’s thirst for raw materials has been an often-raised point of concern, as the Q1 2021 UP Initiative’s Raw Material Sourcing in Batteries theme discussed.
Chile, as the world’s largest supplier of lithium, faces water scarcity as a result of mining activities, for example, while the Democratic Republic of Congo still has not managed to eliminate child labor from its cobalt mines. And these are not the only concerns relating to mineral extraction for energy storage.
Like solar equipment, relying on recycled materials for the energy storage sector is not a long-term, realistic option. The development of the electric vehicle (EV) sector alone is demonstrating this. As Wood Mackenzie noted in a June update, while recycling may relieve some pressure on the supply deficit of battery raw materials, it cannot meet demand.
“The amount of production scrap or EVs coming to end of life will never be able to meet demand while demand continues to increase. There needs to be a push in expanding sourcing while maximizing the recycling sector to ease the deficit,” said research analyst Max Reid.
While lithium-ion batteries remain a key focus, particularly in the EV sector, alternative battery technologies, like redox flow and sodium-ion batteries, are emerging, as the August edition of pv magazine reported. Hydrogen also continues to gain ever more popularity. Diversification is good; however, the sustainability of the materials is still a concern – regardless of the technology.
Loose threads
In Q4 2022, pv magazine’s UP Initiative will focus on material resources, looking at what is being done to eliminate or reduce use of materials like precious metals in solar and storage products, how recycling can play a role, what circular economy strategies are being developed, and what policies are needed to tie all these loose threads together.
UNSW’s Alison Lennon neatly places the topic in terms businesses can understand: “Going forward, manufacturers will consider sustainability because it will affect their bottom line. It’s going to become expensive if you have to source a material that’s in limited supply because its cost is going to go up.”
This content is protected by copyright and may not be reused. If you want to cooperate with us and would like to reuse some of our content, please contact: editors@pv-magazine.com.