Clean heating has been a demand of environmentalists for decades. “Heating is by far the largest producer of CO2 in the household,” reports Germany’s Federal Environment Agency. But there is a wide spread of emissions intensity between heating technologies. Some homes are heated by burning oil or gas and are thus responsible for high CO2 emissions. Others have already have a heat pump, which emit significantly less CO2, depending on the electricity mix used. At least, that is, in theory.
Urban Solar
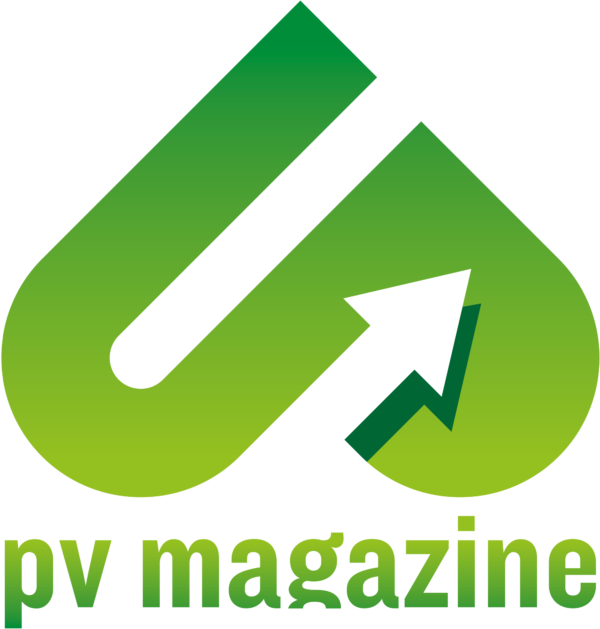
While the installation of a heat pump in a new building is straightforward, as a heating concept is drawn up at the planning stage and the individual components are coordinated with one another, the situation is different in existing buildings. In existing apartment buildings and large homes, the challenge is greater. In buildings in which conventional heating systems are already in place and the radiators require high flow temperatures, it is difficult to switch to a heat pump system. Manufacturers are therefore working on several avenues to extend their capabilities to better serve existing buildings.
There are still many prejudices against heat pumps, even in new buildings or modern existing buildings. “But the heat pump is better than its reputation,” says Ferdinand Schmidt, a researcher on heat pumps at the Faculty of Mechanical Engineering at the Karlsruhe Institute of Technology (KIT). Over the past 20 years, heat pump annual coefficients of performance (COPs) have increased significantly, especially for air-based heat pumps. Here, the average over various installation conditions and devices is now 3.1, albeit with a wide range of COPs between 2.5 and 3.8.
However, this does not make them competitive on price, at least not today in Germany. Competitiveness is influenced heavily by high German electricity tariffs, around €0.30/kWh for electricity, compared to an equivalent of €0.06/kWh for gas, the scientist explains. “For the same energy output per euro, you’d need an annual coefficient of performance of five, and you can’t get that in existing buildings.”
Flow efficiency
Heating systems in old buildings often require high flow temperatures of 70 C to 80 C, or even higher. If the temperature is lower, the heating output drops drastically. The relationship is logarithmic and applies to radiators regardless of their age, explains Alexander Lyssoudis, a member of the board at the Bavarian Chamber of Civil Engineers in southern Germany. “At 10 degrees less in the flow, the heating capacity is only one-third, which means two-thirds of the heating capacity cannot be provided.”
Lyssoudis says achieving higher flow temperatures is the wrong approach for heat pumps to achieve the required performance, because reaching these temperatures comes at the expense of efficiency. A heat pump with a maximum flow temperature of 35 C, for example, can deliver coefficient values of more than six, but only 2.4 in a temperature range of 60 C.
Schmidt has seen something similar. Although there are heat pumps on the market that deliver 62 C flow, he says that “the coefficient of performance then falls to its knees; at a temperature range of more than 60 degrees, coefficients of performance above two are hard to achieve.”
Schmidt does the math. For a temperature swing between the heat source and sink of 60 Kelvin, the temperature swing in the heat pump’s refrigerant circuit is around 70 Kelvin. With a heat pump Carnot COP of 0.5 – that is, the COP is half the thermodynamically possible maximum – and an evaporator temperature of -10 C, the COP is 2.38. A heat pump can be designed for this. However, the refrigeration circuit is typically designed to the operating points required by existing standards, and then the Carnot COP in the extreme point example would not be 0.5, but perhaps 0.4. The resulting COP would then be 1.9.
However, it depends very much on the refrigerants used as to what is achieved in practice. The thermodynamically achievable limit is set by physics, or more precisely by the second law of thermodynamics. This gives a theoretical maximum for the efficiency and thus for the maximum COP, which corresponds to the reciprocal of the Carnot efficiency. However, technically feasible COPs are below this. The formula also shows that the higher the required temperature range, the lower the theoretical limit for the maximum coefficient of performance – which explains Schmidt’s result.
HFC refrigerants
Currently, manufacturers are trying to get the supply temperatures up with other refrigerants at an acceptable efficiency. This is not a trivial challenge. According to Lyssoudis, the hydrofluorocarbons (HFCs) still in use only work acceptably up to about 50 C to 55 C, so the annual performance factor doesn’t drop well below three.
“Every degree of flow temperature above the ideal value of 35 C reduces the efficiency of the heat pump by 4%,” the researcher explained. He gives an example: A heat pump with the HFC R410A has a heating capacity of 17.2 kW and a COP of 4.71 at a heat source temperature of 0 C and a required flow of 35 C. If the flow is to be 55 C, the same heat pump has a heating capacity of only 16.5 kW and a COP of 3.01. If one goes a bit further to 62 C in the flow, the COP then drops to 2.58.
However, HFCs will be phased out. The Global Warming Potential (GWP) of refrigerants currently still in use is in the order of 2,000, which means that if 1 kg of the substance is released, this corresponds to around 2 tons of CO2, according to Germany’s Central Association for Sanitation, Heating and Air Conditioning, which also deals with refrigerants.
“If I have three to 5 kg in my system, and they escape into the atmosphere, then I can also heat my house with oil for one to two years, which has the same effect,” says Matthias Wagnitz, a consultant for energy and heating technology at the association. This only happens in the event of an accident, he notes, but the risk exists.
There are few climate-friendly refrigerant alternatives. Newer “fourth-generation” substitutes such as tetrafluoropropene may have a low GWP, but they only work if other disadvantages are accepted, explains Johannes Brunder, a research associate at the Institute for Building Energetics, Thermotechnology and Energy Storage at the University of Stuttgart.
“The substances decompose quickly in the air, are then no longer there in their original form and are considered degraded,” says Brunder. “However, the degraded products contain toxic and corrosive pollutants that are no longer degradable, such as trifluoroacetic acid, and possibly also highly climate-damaging degraded products.”
Higher temperatures
Several manufacturers, such as Vaillant and Viessmann, now use propane, which allows higher flow temperatures. “This has a GWP 100 of just 0.02 according to the sixth IPPC status report published in the summer,” explains Viessmann press spokesman Wolfgang Rogatty. Previously, a value of three was assumed, which can still be found in numerous sources.
The new Viessmann product, which contains 2 kg of propane, is scheduled to go into series production in early 2022. Property owners will have to sacrifice 1 to 2 square meters of garden space for the outdoor unit. “We can use it to create a flow of 70 degrees even at –15 degrees outside without an electric heater, but it can be included for extra cold days just to be on the safe side,” Rogatty promises. Under standard conditions according to EN 14511, the COP is just above 5.4.
Lyssoudis is familiar with the use of propane, and finds it problematic. For the heat pump to work, the gas is in the circuit at a slightly higher pressure. Because of its high flammability and the fact that it is a heavier-than-air gas, a propane system in the basement of a residential building is dangerous.
Lyssoudis explains: “There are various regulations that add up to make filling problematic, but there is no general ban.” Still, he says that he’s certain that propane will not catch on, despite its thermodynamic properties.
Lyssoudis sees another refrigerant as having an advantage over propane: CO2. It would easily reach temperatures above 60 degrees, but requires high pressures, Brunder suggests 100 bar, in the refrigeration circuit – requiring increased technical effort.
“Because of the high pressure, the overall system is inefficient and expensive,” the researcher says. For manufacturers, CO2 is not preferred. Not only does the heat pump have to generate the high pressure, “we then also need more massive materials, which drives up the price of the equipment,” Rogatty adds.
Ammonia is often used as a refrigerant, but here too there are challenges. “I don’t want that in the house, it’s highly toxic and corrosive,” Lyssoudis says. However, there are ways to use the refrigerant outdoors. An attractive alternative, Brunder suggests, are cycle compression heat pumps that use ammonia/water. These would be suitable for larger capacities of 500 kW to 20 MW. “For heat networks in neighborhoods, this is a conceivable solution – even in existing buildings.”
Theoretical limit
Brunder calculates that a system with a supply of 60 C at an outside temperature of 0 C has a theoretical coefficient of performance of 5.5. “If you look at the properties of the refrigerants, systems with the currently used refrigerant R410A, an HFC, come in at a maximum of 3.5, with propane at 3.9 and with ammonia at 4.5.” Given this, there’s still room for improvement.
However, he advises against looking solely at the COP. The compressor’s grade, a measure of a machine’s internal losses that is often confused with efficiency, also plays an important role, he says. “The highest theoretical value does not have to be the most practical,” he says. Here, Brunder suggests, degrees of quality of 50 to 80% are realistic.
Instead of looking for new refrigerants, manufacturers could also improve the processes in heat pumps. “If you cool down the liquid refrigerant after the compressor and heat the gaseous one after the evaporator, that increases efficiency,” Brunder says. With propane, he says, the approach works well.
Smaller temperature differences also help. A lower temperature difference between the internal and external circuit of 2 Kelvin instead of 5 Kelvin is immediately noticeable. “You then get a flow that is three Kelvin warmer without changing anything in the refrigeration circuit,” Brunder says. The disadvantage is that the heat exchanger has to be somewhat larger.
Changes to the compressor, such as an intermediate injection with liquid refrigerant, could also increase the temperature level of the usable heat and thus the flow temperature. Viessmann, for example, offers intermediate steam injection for ground-source heat pumps. In this case, two heat pumps are interconnected. A certain amount of refrigerant is then diverted within the refrigeration circuit and injected into the heat pump’s compressor.
“We can achieve a flow of 73 degrees and a maximum capacity of 274 kilowatts with a brine-to-water heat pump for apartment buildings and commercial businesses this way, but larger capacities are also possible with air-to-water systems,” Rogatty says. The brine-to-water pump’s COP is 4.4 at B0/W35, according to EN 14511.
Over the long term, the refrigerant is one of the most important ways to achieve higher feed rates with acceptable efficiency. Rogatty doesn’t see the end of COP improvements even after Viessman’s new heat pump is on the market.
“There are still opportunities for even higher efficiencies, at least in theory; a few years ago, you wouldn’t have thought of using propane as a refrigerant either, because you didn’t know certain techniques yet.”
By Jochen Bettzieche
This content is protected by copyright and may not be reused. If you want to cooperate with us and would like to reuse some of our content, please contact: editors@pv-magazine.com.