Mr. Suleiman, your company is providing consultancy and procurement services for PV manufacturers in the Middle East. What kind of solar industry is being established there?
The Middle East is frequently in the news for large-scale PV power plant project awards and record PPA prices. However, there is less coverage on the manufacturing side and the exciting developments happening therein. In the last five years, we have seen the rise, and closure, of a few producers in the region. In general, you can divide the manufacturers into different categories: existing local producers; new local entrants; former European module manufacturers; European developers; Chinese investors and manufacturers; and Indian investors and developers.
What is differentiating these players?
The case of existing local manufacturers includes those who have been around since the 2000s, before the rise of solar as a real contender. In this category, there was Microsol/Solon in Fujairah, in the UAE, with a 200 to 300 MW cell and module capacity, which no longer seems to be in real operation. In Jordan, Philadelphia Solar has been producing PV modules since 2007 with a 60 MW production capacity. There are few other very small-scale manufacturers in Lebanon and Egypt as well.
New local entrants are tricky to measure, as many of these aspirations fail during project development phase, predominantly due to lack of sufficient working capital. Often the initial CAPEX for a module manufacturing facility isn’t high, but this blinds investors from comprehending the real working capital involved. There are a few upcoming local manufacturers that may have better luck, because they figured out a unique market opportunity that they are willing to focus on and carve for themselves a niche.
If you are not planning to differentiate and establish a winning strategy, and stick to it, then it is impossible to survive as a small local manufacturer with abundant Chinese modules in the area. For small manufacturers, I mean those with a capacity of less than 100 MW.
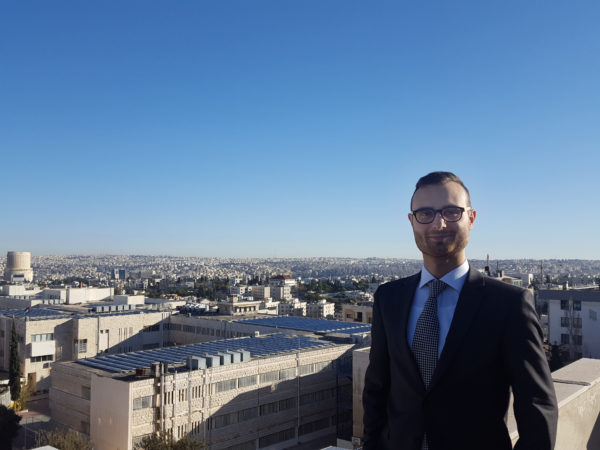
SIPCO
What about the European manufacturers you mentioned?
These are making use of the Middle East+ proximity, free zones, and cheaper labour to remain competitive and relevant. In this scenario, a European manufacturer would move part or all of its existing production lines to places like Jordan and the UAE to produce with a similar Bill of Materials (BOM) and deliver to their existing customers in Europe.
Wiosun in Aqaba is one such example that has a strong focus on quality and reliability through a high-performance BOM. Often the producer teams up with a local investor, and this has the advantage of minimizing risk, access to regional projects, and, if done right, selling shares at a premium. These types of manufacturers have a unique advantage of experience, know-how, and existing customer base. However, special care must be taken to source knowledgeable staff and transfer the know-how properly, to ensure similar high-quality output and effective decision making. This, however, seems to be the most difficult part for most of our clients and that’s where we step in to support.
European developers are parallel to European manufacturers, but with different end-goals. They set up completely new ventures to supply modules for their projects and avoid minimum import prices (MIP) imposed on Chinese modules. In one case, an existing local production line was acquired. In doing so, they can develop projects relatively cost effectively compared to sourcing modules from European manufacturers and fulfil their PPAs with acceptable margins. This can also be considered as “new entrant”, because some of these developers have no history in PV manufacturing. Currently, there are two new such players in Jordan in the project development phase and a few others in the UAE and Saudi Arabia.
You also mentioned Chinese manufacturers and investors.
MIPs on Chinese modules are also pushing Chinese manufacturers to operate in the region. In this business model, like in the case of European developers, Chinese manufacturers set up production bases in the area to access markets that are becoming increasingly difficult, even via proxies such as Taiwan and Malaysia.
In Turkey, you have observable cases of these, while in the Middle East at the moment there is Maysun Solar, which recently entered operation in JAFZA Dubai with a nameplate capacity of 40 MW to be expanded to 100 MW in the future. Furthermore, there’s ChangZhou Almaden subsidiary Almaden MENA, which focuses on glass-glass modules.
Other such ventures are in the planning in Oman, however, there is no clear schedule for some of these projects. This business model will most likely depend also on contract manufacturing for the larger Asian manufacturers. However, it has to be noted that this may not be a sustainable long-term strategy. As we have seen how the European Commission has made custom clearance procedures very difficult for modules imported from Malaysia or Taiwan, such punitive measures can also be applied to modules imported from the Middle East.
Are the Indian manufacturers better positioned than others, due to the improvement of India’s relationship with the Arab world?
Indian investors and developers have set up new production lines in the UAE or Bahrain to cater to their project developments in India. Some of these have failed, some have succeeded, and some are too young to judge. The Gulf is a unique place for such players, because of the historic ties and labour availability of the same ethnicity. In some cases, this kind of manufacturer would purchase second-hand production equipment from a European producer at a discount. Then of course there are some outliers such as QSTech of Qatar which seeks to take part high in the PV value chain by producing solar grade polysilicon and expand downstream to cells and modules manufacturing. It would be interesting to see how the landscape will change by 2020 as changes in political situation, trade policy, and investment laws evolve. One thing to keep in mind is that most of the production is intended for export.
The real threat is to small local producers of less than 100 MW who cannot benefit from economies of scale and compete with influx of Chinese modules. As mentioned, the only chance of their survival depends on a winning differentiation strategy and sticking to it, in addition to protective trade barriers such as those by Saudi Arabia’s push for local content policy. SIPCO is taking an active role in the growth of a local PV manufacturing base in the Arab Middle East by supporting investors, managers, and operators of PV manufacturing facilities with turn-key production facilities, technical training, raw material sourcing, and business development services. We achieve this through our global partners, industry insight, technical know-how and experience of delivering solutions to industrial facilities for over 25 years
Is there potential for big players in the local solar manufacturing industry?
Yes. This was one of the trends highlighted. Big manufacturers are opening operations in the region to bypass MIP policies in some countries, such as Europe and the U.S. They can partner with local investors, or acquire existing local production lines and build them up. Whether this is a sustainable strategy is yet to be seen, as trade policies in Europe can quickly change to impose punitive duties on modules from the region. On the other side of the coin are developers who want to have a safer procurement strategy and wish to supply their own projects; these also have potential to take part in the local solar manufacturing industry. But let us not forget that a large majority of the local production is intended for export.
What is the combined capacity of all module manufacturers active in the Middle East? Can you name the largest solar module maker?
Popular content
Around 450 MW of effective capacity, but virtually no one is operating at full capacity. The largest active producer is Philadelphia Solar of Jordan, with nearly 70 MW annual production. Desert Technologies of Saudi Arabia will be in full production very soon, reaching 100 MW per year. It is important to remember that there are many production lines that are lying idle, due to financial distress, outdated technology (3BB stringers), or lack of orders. So that’s why it is important to consider only effective capacity.
Is the lack of a qualified workforce an issue for the Middle Eastern solar industry?
Definitely. Many people think the skilled workforce are the on-line operators who need to be trained about operation and handling, and at most, visual quality inspectors. In our opinion, this isn’t the weak link that needs to be fixed. New production lines that are heavily automated are becoming even more economic, so even new entrants can afford them.
In a future of even higher automation, there is less direct interaction between the production process and operators, and so the skilled level of the operator is not going to play the main role, although it remains an important one. The real trouble we see here are the decisions management takes on BOM or the technical understandings of management level employees. To illustrate, we often are baffled that some technical managers do not pay attention to their BOM and intended application: in some cases, manufacturers are employing non-fluoropolymer based backsheets for modules intended for harsh desert climates where the high UV levels and humidity are no joke. In this case, they employ regular three (or two!) layer polyester-based backsheets that will not survive a quarter of the intended module warranty period.
Ultimately, there is poor judgement on which BOM works best for each location and application. In other cases, some quality managers have superficial understandings of what parameters to pay attention to with regards to raw material sourcing, which results in procurement evaluations influenced by non-standardized test results and marketing gimmicks. These managers enter many training sessions and workshops for professional development, yet the technical capacity building seems to be weak.
How can these issues be addressed?
With proper technical training and capacity building, managers can make more informed decisions that align with their strategic business goals. Of course, not all producers suffer from this problem. Some manufacturers have brought in partners with extensive history and know-how from the PV industry that help them make the right decisions and ramp-up successfully. If they haven’t, then they reach out to us and we support them in this matter.
The other way to address this issue is by educating the public institutions responsible for the development of PV systems. By raising awareness on the latest standards and application-specific requirements, there can also be government pressure on PV system component requirements and help raise the local PV industry to higher levels. Vocational training centres focused on PV manufacturing are also an interesting option that can be considered by governments that wish to create a local PV manufacturing hub and create employment opportunities.
This lack of skilled management level workforce also exists in some EPC companies. We have observed that some installers do not pay attention to the reliability of modules they are receiving. Even if from a Tier 1 manufacturer, they do not consider the role of the BOM or application-specific certificates that are required. Late last year, when module prices dropped so low, we were very worried about the reliability of modules that were installed in the region, as even Tier 1 producers were relying on third-party manufacturers and being lenient on BOM to save margins. We advised some EPC companies to avoid very low-priced modules, in order to keep their projects safe and to ensure reliability of warranties and delivery.
The victim of such a lack of ‘skilled workforce’ is the PV industry itself, because when modules begin to fail and systems break down, the PV technology image is tarnished. This is why SIPCO is now also paying attention to working with developers and end-users by offering EPCM and consultancy services towards reliable, profitable, and safe PV systems.
Hot and arid climates need high quality modules and inverters. Do you believe the Middle Eastern solar industry is prepared for this? Is this the reason why what is currently being produced there is being exported?
The reason for modules being export driven is due to the strategies and business goals of the investors. A considerable amount is exported to India, Pakistan, and North Africa, where high UV and humidity are also prevalent. Another reason is that most of the projects in the region (especially the ones that make headlines) are prime large-scale projects that involve global developers and financers that will rely only on Tier 1 suppliers with sufficient capacities. Many of the local manufacturers will not qualify to supply to these projects, because they are either new or small and, as such, don’t meet the criteria set by these developers and their risk department.
As such, they seek projects abroad where the criteria is more lenient or they cater to their own-developed projects and local demand that is small. This doesn’t mean their modules aren’t of high quality, but rather they don’t meet legal requirements for the big projects that are realized. Indeed, we believe some small local producers produce higher quality and more reliable modules than some of the Tier 1 manufacturers. Especially in countries where positive legislation and economic conditions that promote commercial or residential-scale systems are potential markets for local producers. This is the case in Jordan, where the annual non-utility sector project demand reaches 15 to 20 MW where there is less strictness in applying a ‘Tier 1-only’ path. Other examples are Iraq, Lebanon, and Morocco, although these do not necessarily have strong legislation, but have the right economic environment.
Is the Middle Eastern solar industry ready for these kind of challenges?
Yes. There are people on the ground working hard to get this industry up and running, which involves a lot of effort in spreading knowledge and experience. It is important to mention that all players across the value chain need to build capacity and establish dialogue. Just as the global PV industry goes through consolidation, the local industry, the Middle East, is no exception. We only hope this will lead to a higher level of manufacturing.
Do you believe that mega-solar factories will be possible in the Middle East?
Yes, but in the long-term, and only after serious consolidation occurs and the weak players are out of the game. Currently, it’s not fully clear, as political and legal changes are being closely watched, to fathom what kind of business environment will be created. Will the European Commission apply trade barriers to modules imported from this region? Will government electricity subsidies in the Gulf be fully lifted to promote the growth of small scale PV demand? In addition, the PV industry development in other countries will also influence local players in terms of demand and market access. We don’t believe we will see anything compared to the scale of Asia, but it’s still a young industry here and anything is possible.
Is it possible the trend will also be that of small solar manufacturers that do not exceed 100 to 200 MW of capacity, in order to stay alive, as in Europe?
Yes, this is probably going to be the trend for the near future, until the business environment presents something new. In the past, we’ve heard numerous times that local manufacturers were planning to expand capacity, but nothing has been realized yet. There is too much risk involved and such capacities cannot be realized without a clear strategy that, at a minimum, guarantees orders, such as developers using their own modules in their own projects.
This content is protected by copyright and may not be reused. If you want to cooperate with us and would like to reuse some of our content, please contact: editors@pv-magazine.com.
1 comment
By submitting this form you agree to pv magazine using your data for the purposes of publishing your comment.
Your personal data will only be disclosed or otherwise transmitted to third parties for the purposes of spam filtering or if this is necessary for technical maintenance of the website. Any other transfer to third parties will not take place unless this is justified on the basis of applicable data protection regulations or if pv magazine is legally obliged to do so.
You may revoke this consent at any time with effect for the future, in which case your personal data will be deleted immediately. Otherwise, your data will be deleted if pv magazine has processed your request or the purpose of data storage is fulfilled.
Further information on data privacy can be found in our Data Protection Policy.