Thanks to its potential to boost module power output, half-cell technology – whereby silicon solar cells are cut in half prior to layout within a module – is now an industrially relevant concept being adopted by several leading module manufacturers. Among these is Korea’s Hanwha Q CELLS, which is about to launch a range of modules incorporating the half-cell layout in high powered mono crystalline silicon modules. The modules were first shown at Solar Power International in Las Vegas back in September. Beginning in January, Hanwha Q CELLS will devote a significant portion of its production capacity to manufacturing the new half-cell modules.
This new range, named Q.PEAK DUO, consists of 120 and 144 half-cell modules, incorporating Hanwha Q CELLS’ existing Q.ANTUM technology – based on the passivated emitter rear contact (PERC) concept; and further innovations including a six busbar set up, and connecting the cells with round wire rather than ribbon, as well as the half-cell layout. “In parallel to continuing our development of the Q.ANTUM cell itself, we thought about what we can add on the module level,” explains Hanwha Q CELLS Director of Corporate Communications Jochen Endle. “We did the six busbar technology, and the half-cell layout. That brings us into competition with much more expensive technologies for high-end power class PV.”
Push for power
Chief among the reasons for the growth in half-cell technology is the potential to provide a power boost at module level. In an example provided by Fraunhofer ISE, sample modules incorporating the full cell and half-cell layout were compared when using the same total cell power. The cells utilized have a power rating of 330 W, this translated to module power of 316.7 W for the full cell module, and 325.2 W for the half cell module, an increase of 2.7%. The modules are otherwise identical, although the half-cell module is 1.8% larger, as the design naturally means more cell gaps. Therefore, the efficiency boost is not as strong as the power boost, increasing from 18.84% to 19.12%.
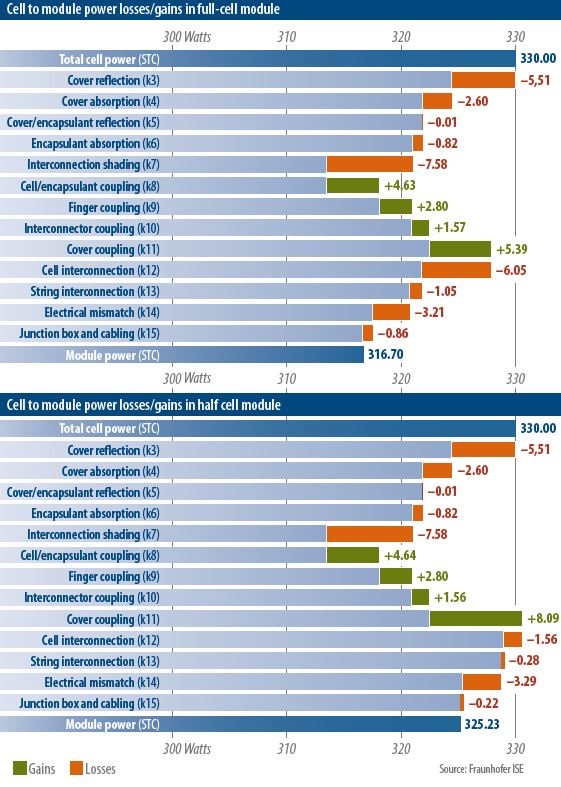
As shown in the graph, the largest difference in cell to module losses/gains comes at the cell interconnection stage, where a 6.05 W loss in the full cell module is reduced to 1.56 W in the half-cell. Cutting cells in half also halves the electrical current, meaning that resistive losses decrease. On the other hand, in half cut cell modules, losses due to the area lost between the cells is increased. In half cells, there are just under twice as many cell gaps as in full cells. These losses are partially recovered by multiple reflection of the light. This recovery is higher in half cut cells than in full cell modules, as the losses are higher. “When light falls into the intercellular space, it is partially reflected again and in turn partially reflected back to the cell at the front glass-air interface,” explains Ulrich Eitner, head of the photovoltaic modules group at Fraunhofer ISE. “In glass-glass modules, for example, this gain does not occur.” As round wire for the cell interconnection can further increase the recovery due to enhanced reflection compared ribbon, it makes sense that Q CELLS also adopted this interconnection concept.
Hanwha Q CELLS also reports a 3% power increase, attributable to the half-cell layout, in its latest module offering. The largest of the range – the 144 half-cell monocrystalline Q.PEAK DUO L-G5.2 comes with a power rating up to 395 W. “The first big advantage is the higher power of around 3%,” explains Maximilian Schurade, Director of Technical Marketing Support at Hanwha Q CELLS. “This is the effect of the half-cell itself, and the different interconnection, because you reduce the resistive losses in the module.”
Another reported advantage of half-cell modules is increased mechanical stability. “The half-cut cells are smaller, so it’s much harder to break them,” continues Schurade. He also notes that Hanwha Q CELLS choice of process for cutting the cells does not bring additional weakness to the module, and that the improved mechanical stability allowed the company to improve the maximum yearly degradation specified in its warranty from 0.6% to 0.54%.
The slight increase in the size of the module, according to Hanwha Q CELLS at least, appears to be negligible “it’s 15mm longer, this is not really an issue though,” says Schurade. “The width is more important for most installations, so the additional 15 mm in length is not really an issue for our customers.”
Separating the cells
Alongside half-cells, innovative strategies for connection can further reduce cell to module losses. Hanwha Q CELLS has opted for round wire technology in place of ribbon, which it says achieves a power increase of around 2%. According to teamtechnik as well, there is an advantage to using roundwires, but also some additional challenges to be wary of.
“With a round wire you will get more reflection of incoming light. Light hitting the round wire is reflected back to the glass panel, and from the glass back to active surface of the cell,” says Kramer. “The challenges are the reduced contact area on the busbar, adhesion of the wire on the cell, and the alignment – since you have less contact area it might move around a bit. Handling the round wire is a little more tricky compared to the flat ribbon, but it can be done.”
The Q.PEAK DUO range features six busbars, which further reduces resistive losses in the module, by reducing the distance electrons need to travel once captured. The move to six busbars further demonstrates Hanwha Q CELLS’ desire to push as much power as possible out of its module. In teamtechnik’s view, the gains seen from such a move are not large enough for many manufacturers to take note. “The main reason you change the number of busbars is to reduce resistive losses,” says Kramer. “The biggest gain came from three to four. There is another increase from four to five, and from five to six. But it gets smaller each time, and you are adding more complexity to the process.” Hanwha Q CELLS estimates that adding a sixth busbar by itself can bring about a 0.5% increase in power.
Mono vs Multi
When it comes to PERC, the issue of light induced degradation (LID) has been a major one, which still holds many manufacturers back from producing PERC with cheaper multicrystalline silicon. At the pv magazine Future PV event, held during Intersolar Europe, Hanwha Q Cells presented measurements to prove that they have solved the problem.
A surface texturing issue which prevented the use of cheaper and more efficient diamond wire sawing in multi-Si led to a period of strong growth in mono. Now that solutions to this are commercially available in the form of black silicon and other processes, many manufacturers are shifting towards multi once again.
Hanwha Q CELLS, on the other hand, chose to add mono capacity to its portfolio in late 2016 and is now adding more mono capacity for the Q.PEAK DUO module line. The company, however, is keen to stress that market forces are what’s behind this. “While we can say that we have added mono to our portfolio at a large scale, this does not mean a shift away from multi, ” says Jochen Endle. “Our belief is that there is demand and justification for both technologies.” Accordingly, the company is in the process of converting most of its capacity for both mono and multi-Si (expected to be 8 GW at the end of 2017) to produce its Q.ANTUM products, based on PERC technology, stating that demand for high power classes is its main reason for doing this.
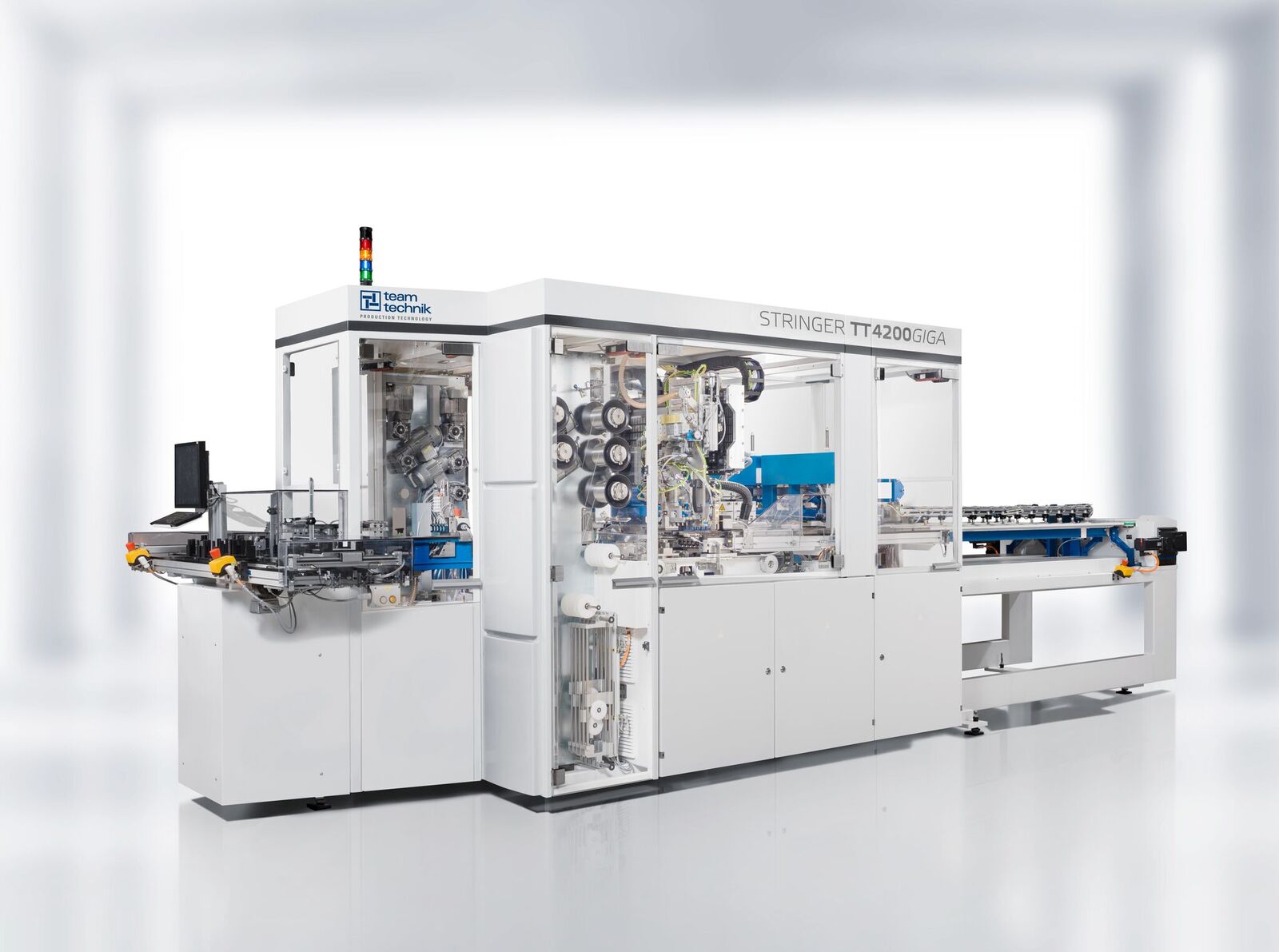
Next to Light induced degradation (LID), light elevated temperature induced degradation (LeTID) also has the potential to cancel out PERC technology’s increased efficiency, and even to bring it lower than that of a standard back sheet foil module. While tools have been successfully developed to minimize these degradation mechanisms in mono PERC production, and are in development for multi cells (see pv magazine 06/2017, p.92), Hanwha Q Cells Q.ANTUM technology features its own anti LID & LeTID mechanisms.
“When we first started with mono for our current Q.PEAK module series, some people were thinking ‘OK, you are doing multi-PERC and you cannot control LeTID, so you shift to mono,” continues Endle. “That is not the case, we do stick to multi production, and we do control degradation very well in multi.” Moreover, he is certain that the company’s own experience in developing PERC through its Q.ANTUM multicrystalline technology was an advantage as it moved in to the market for mono and now continues to move into the market for mono half-cell products: “The thing with these effects, is that this is really something where you need to have experience, and understand the effects in depth to be able to control them reliably.”
This content is protected by copyright and may not be reused. If you want to cooperate with us and would like to reuse some of our content, please contact: editors@pv-magazine.com.
1 comment
By submitting this form you agree to pv magazine using your data for the purposes of publishing your comment.
Your personal data will only be disclosed or otherwise transmitted to third parties for the purposes of spam filtering or if this is necessary for technical maintenance of the website. Any other transfer to third parties will not take place unless this is justified on the basis of applicable data protection regulations or if pv magazine is legally obliged to do so.
You may revoke this consent at any time with effect for the future, in which case your personal data will be deleted immediately. Otherwise, your data will be deleted if pv magazine has processed your request or the purpose of data storage is fulfilled.
Further information on data privacy can be found in our Data Protection Policy.