Top-tier Chinese tracker component suppliers have adopted the most stringent international norms for quality control, are adept at cooperating with client quality control agents, and have sought out multiple independent certifications of quality.
Among top tracker component makers in China is Arctech Solar, which embraces quality in a holistic manner. “We have a quality inspection process, and a quality control team responsible for checking that each component — and the whole system — meets a certain threshold,” Guy Rong, president of Arctech Solar’s international business. “The quality control team also maps out the entire process quality of analysis and engages in continuous improvement of the system,” he says.
Boots on the ground
Despite the best practices of such leading PV industry manufacturing in China, quality varies widely across companies, experts say. “China is a market that offers you the possibility of buying at different price and quality levels, but we choose suppliers with a proven track record and field experience, who can demonstrate that their technology is well-tested,” says Maria Barbarin, Contracts and proposals manager for Spain based tracker manufacturer, STInorland.
World-class quality is available in China, alongside other cost/performance options. “In China the quality of a given component varies significantly from manufacturer to manufacturer, because in some cases manufacturers are top-notch and world-class, but in other cases they are not.” says Ralph Romero, Senior Managing Director of U.S. EPC company Black & Veatch.
STInorland, which manufactures trackers in China, among other countries, reckons that there may be four levels of local inspection at work in any given factory. “First, we have the manufacturer's own inspectors; second, we have our own quality team based in the factories; third are third-party inspectors; and a fourth level may come from our customers, who are allowed to visit our factories, and to carry out their own audits and product checks if requested,” says Barbain.

Elusive standards
The quality challenge in China goes beyond the QC transformation of individual companies, as well. “There isn’t a standard that you could point to across the board, that means it’s pretty good. Since we haven’t seen that country standard arise yet, product quality requires that you have a presence on the ground, and that you conduct random inspections,” says Romero.
Many top-tier China PV component suppliers seek out in-factory inspections by Germany’s TÜV, the global leader of such quality assurance. Among other global on-site inspection services providers, “Arctech has worked together with institutions like Clean Energy Associates (CEA), the Australian Photovoltaic Institute (APVI), and Lloyd’s Register Quality Assurance,” Liu says.
These groups confirm the manufacturer’s adherence to in-house quality control, which might include Arctech’s key steps, Incoming Quality Control (IQC), Product Capability Testing, Process Quality Control (PQC), Final Quality Control (FQC) and Outgoing Quality Control (OQC).
Soltec, another Spain headquartered tracker manufacturer, says that its third-party providers of quality auditing in China — and elsewhere – also include SGS and Bureau Veritas, along with an in-house staff of 10.
Documenting sub-component quality
A major problem in the past for China quality control for PV components was the failure to track the quality and source of sub-components sourced from varied types of company. “Suppliers to suppliers are hidden in the marketplace,” says Mike McMullen, Cofounder of PowerGuard Insurance, a third-party warranty issuer based in San Francisco.
“We have seen may issues with sub-components despite alleged QC procedures in place,” adds Black & Veatch’s Romero. “When you get on the ground in these cases, you find that QC is not being implemented, or that the responsible individual is not well trained,” he says. “In one case when we were looking at coatings on metals and built steel structures, including a custom component for a tracker, the supplier claimed that they measured the coating thickness by a non-destructive method, but we found no equipment on site to do that,” he says.
To hold sub-component suppliers accountable, Arctech demands ‘cradle-to-grave’ documentation. “Basically, we provide our customers with a certification of origin (CO) for each shipment batch,” says Liu. “More specifically, we can provide our clients with tracked details of raw materials, such as mill test certificates, steel labels, bath numbers and shipping documents,” she adds.
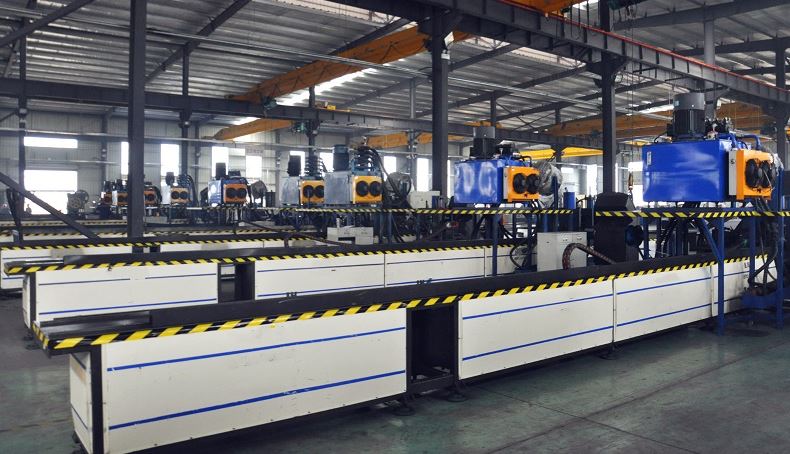
Warranties back quality measures
Warranties for tracker components may come directly from the tracker company, directly from the component suppliers or from third-party warranty providers. Arctech’s warranties reflect global warranty standards, Liu suggests: “The limited warranty for our horizontal single axis solar tracker is five-years and ten-years for the repair, replacement or a refund remedy for the whole system and structural components,” she says. “For solar module mounting structures, Arctech warrants a 10-year repair, replacement or refund remedy and 20-year service,” she adds.
Soltec offers a warranty of 10 years on structural components that may come from China, Brazil, the U.S. or Spain. The warranty is five years on drive components and electronics, including the controller electronics assembly, manufactured in Spain. “The tracker mounting brackets are the most elaborate steel component, and are fabricated and tested in Spain,” says Vestal.
Not all suppliers manufacturing in China have the balance sheet strength or longevity to be perceived to adequately stand behind their product warranties, however. Thus, the need for third-party warranties arises.
“Thriving manufacturing companies in China now see the need for third-party warranties. They help them spec out the bottom feeders, so they don’t have to bid against the lowest-cost producer,” says McMullen.
While the component makers may pay for third-party warranties, tracker companies generally don’t. “Most tracker companies don’t carry third party warranties, rather, they are driven by a financial institution making an investment in a large project,” says McMullen.
While there are varying types of insurance to cover potential performance situations, insurance does not typically cover the cost of hardware replacement. “Third-party warranties are expensive, and warranties are an area that most insurance companies don’t want anything to do with,” McMullen notes.
One way that third-party warranties are helping to improve quality for those China manufacturers that use them is the analysis of failure reports. When a component fails, and a warranty claim is made, an incident report flows to the quality control office of the manufacturer. When there are patterns in claims, there is an opportunity to chase the cause to ground, McMullen notes. His company recently acquired a quantitative analytics company that will help point out such manufacturing anomalies for clients.
Obscure origins
With the current climate of trade war between China and the United States, the challenge of documenting the quality and source of solar components will only become more difficult, the experts agree.
“With trade issues, the manufacturing geography shifts, because a Chinese manufacturer may establish a factory in Malaysia or Vietnam, so now there are new facilities to visit and verify,” says Romero. “Just because a product has the same label doesn’t mean it has same quality. We see this quite often,” he says. Black & Veatch has offices in Beijing, Hong Kong, Jakarta, Singapore and Bangkok to lend to its regional perspective on quality.
At times vertical integration, which might involve the purchase of a tracker company by a steel maker, a custom electronics manufacturer or another global company type does not assure that all products from all locations are equal, suggests Romero. “A lot of global manufacturers set up different country operations as franchises, so quality control may not be identical,” he says.
Identifying committed suppliers
Quality-committed Chinese solar component suppliers seek out ISO9001 international quality management certification to set them apart from other players. Quality leaders also seek out quality certifications from independent agencies around the world. Arctech, for example, was certified last year in the Witness Test Data Program of TÜV Rheinland. “We have also obtained certifications from Underwriters Laboratories (UL), Cermak Peterka Petersen (CPP), and Intertek’s Electrical Testing Laboratories (ETL) to safeguard the quality of the tracker system and to provide a stable base as a reliable partner for our global customers,” says Liu.
Still, a certification is a general stamp of approval for the practices of a given company, as opposed to the inspection of a particular part that may be specified in a large tracker proposal. This is where bankability studies provide comprehensive risk analysis.
“Certification is a good sign, but by no means is it as sufficient a requirement for project success as a bankability study,” says Romero. “This is not merely a financial study, it is a hard core technical analysis.”
“The purpose of a bankability report for a tracker touches on five areas,” says Romero. “First, whether the design meets the tech specs; second, understanding whether the tracker in the field performs to tech specs; third is understanding whether the company can consistently make trackers that fit these performance specs; fourth is understanding installation, parts, and budgets; and fifth is determining whether a company as a whole is positioned to meet its objectives,” he enumerates. “The detail focus is on the manufacturing quality, with a set-by-step review ranging from the incoming inspection of materials to the shipment of finished goods,” Romero concludes.
This content is protected by copyright and may not be reused. If you want to cooperate with us and would like to reuse some of our content, please contact: editors@pv-magazine.com.
1 comment
By submitting this form you agree to pv magazine using your data for the purposes of publishing your comment.
Your personal data will only be disclosed or otherwise transmitted to third parties for the purposes of spam filtering or if this is necessary for technical maintenance of the website. Any other transfer to third parties will not take place unless this is justified on the basis of applicable data protection regulations or if pv magazine is legally obliged to do so.
You may revoke this consent at any time with effect for the future, in which case your personal data will be deleted immediately. Otherwise, your data will be deleted if pv magazine has processed your request or the purpose of data storage is fulfilled.
Further information on data privacy can be found in our Data Protection Policy.