Passivated Emitter Rear Contact (PERC) technology is becoming a standard technology for high efficiency cells, but light induced degradation (LID) is a major problem.
If LID is not treated, degradation can be up to 10% in the first month after installation. To combat this, cell manufacturers add an LID treatment process at the end of the cell production line to eliminate the effects.
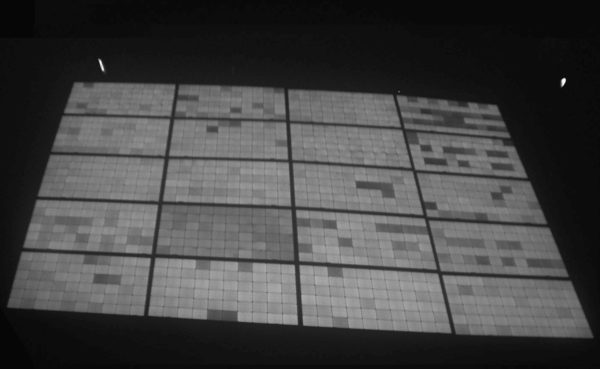
Jay Lin
Ideally, the LID effect should be eliminated for all cells, but from our experience in the field of EL inspection, we observed that half of all PV modules still have LID problems. Why can the LID effect not be completely removed? To explain this difficulty, we first need to understand the LID behavior of the cells.
Quality roundtables
Mono cells
For mono cells, whether using PERC, or conventional, technology, boron oxygen (B-O) LID is the dominant effect when the cells are exposed to sunlight. The current treatment in production lines is to deal with this type of LID. However, there are also other types of degradation, like light and elevated temperature induced degradation (LeTID) or others, that cannot be treated in production yet. Therefore, the discussion here is mainly about boron oxygen (B-O) LID.
LID regeneration occurs under high temperatures, when the cells are exposed to light or current injection. Figure 1 plots the whole process of LID regeneration. At the beginning, the power degrades from point A to B (degradation). If the process continues, the power starts to increase from point B to C (regeneration).
However, if the process stops at point B, the cell will go back from point B to A in the dark (annealing). When the annealed cells are re-exposed to light, the LID process will restart, from point A to B. Therefore, the LID elimination treatment must be done over point B, otherwise it is very unstable and goes back to point A after a period of time.
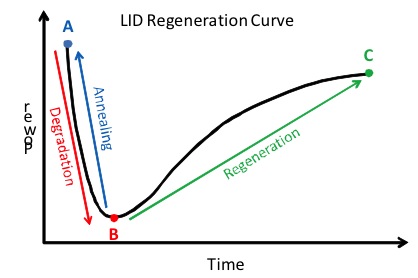
Image: Jay Lin
Balancing act
The best treatment is to finish the whole regeneration, so the power returns to higher levels and there is no further LID effect. But it takes time to complete the process, and production capacities will be greatly influenced. Manufacturers need to find a balanced way to treat the LID effect at an optimum level, i.e. in the most cost effective way.
If the treatment stops between point A and B, the LID effect is not completely removed, and customers will suffer LID afterwards. As such, the process level below point B is considered insufficient. The optimum treatment level should be somewhere between B and C, where the customer will earn slightly from the regeneration afterwards (although it takes a long time).
Here comes the problem: There are thousands of cells produced on production lines every day, and each cell has different characteristics. Additionally, LID regeneration equipment does not treat every cell uniformly. As a result, every cell is at different LID regeneration level after treatment.
The distribution of the treatment level is usually normal, as shown in Figure 2. In this figure, most of the cells are treated at the S3 level, while some of them reach the S4 level, and only some, the S2 level. The cells below the S2 level are considered to have been insufficiently treated. In this example, 1% of cells are below the S2 level.

Image: Jay Lin
1% below S2 level doesn’t sound too bad, as it means 99% of the cells have no LID problems. But, when the cells are transferred into 60-cell modules, what percentage of the modules are affected?
The maths
Let’s do the maths: When 99% of the cells have no LID problems, then the percentage of modules with no LID is (99%)60, or 54.7. That means 45.3% of modules have at least one LID cell inside, and one cell is enough to influence the power of the whole module. The risk of hot spots also occurs.
This percentage also meets our observations in the field: Around half of the modules are LID infected, when we do on site EL inspections.
To improve this situation, manufacturers should either enhance LID treatment levels, or make LID treatment more uniform, so fewer cells fall below the S2 level in Figure 2. If 0.1% of cells are below the S2 level, just 5.8% of modules will be affected, which is much better than the current status.
Jay Lin is the Chief Consultant of PV Guider Consultancy. He has 14 years experience in PV research, manufacturing and systems. PV Guider provides quality assurance services for PV investors, insurers and banks. With the experience in factory audit and systems inspection, he is specialized in connecting failures in the field with errors in production.
The views and opinions expressed in this article are the author’s own, and do not necessarily reflect those held by pv magazine.
This content is protected by copyright and may not be reused. If you want to cooperate with us and would like to reuse some of our content, please contact: editors@pv-magazine.com.
By submitting this form you agree to pv magazine using your data for the purposes of publishing your comment.
Your personal data will only be disclosed or otherwise transmitted to third parties for the purposes of spam filtering or if this is necessary for technical maintenance of the website. Any other transfer to third parties will not take place unless this is justified on the basis of applicable data protection regulations or if pv magazine is legally obliged to do so.
You may revoke this consent at any time with effect for the future, in which case your personal data will be deleted immediately. Otherwise, your data will be deleted if pv magazine has processed your request or the purpose of data storage is fulfilled.
Further information on data privacy can be found in our Data Protection Policy.