pv magazine: What drove Opes Solutions to develop this off-grid module using lead-free solder?
Robert Händel: The module was developed at the request of our customer, Biolite. They are a very innovative company and they asked us for it. They use modules in small solar home systems in several African countries. In Africa there is a high awareness of environmental damage from components. They [Biolite] have experience, for example, in East Africa, where lead-containing car batteries have been dumped irresponsibly, leading to lead seeping into the groundwater and cases of lead poisoning.
Lead in c-Si modules
And what challenges are created by eliminating lead from your production?
The challenge is always how to do this without increasing the cost. It’s also a very price-sensitive market. We started to look into it and you have all these materials like zinc, copper, silver, nickel and more, that you can make into alloys.
The driver is, if you have to solder hotter – say, going up to 360 or 380 degrees Celsius – then you get more stress and more breakage on the cells. But you also get better bonding with most of the alloy components. The challenge is to get the temperature down without lead and we now solder lead-free at 300 degrees [Celsius], just a little over 280, which is the standard temperature.
The standard module industry has this 1.5 newton per millimeter pulling force test after damp heat and thermal cycling. That’s a decisive thing over time – how strong your ribbon connection is – and can prevent your solar module from power losses in the future.
We have now found a good solution where we match the cost required for the market and the pulling forces required in testing. And we have one more advantage: We don’t have full data on this yet but in off-grid modules you don’t have long strings with high voltages and currents going through your connection points. We don’t go up to 1,000 volts and 8 amps. And when you have a 6 W or a 10 W module in a single application, there is much less stress there on these parts.
And in the off-grid market generally, we want to introduce lead-free over time. It’s not required by law at this point but customers ask about it and we talk about it. We also have products that don’t have the same lifetime requirements as a standard module.
How have you replaced lead in the solder?
Basically, you experiment with the mixture of the alloy, the percentage of different materials. We have some parts – copper and bismuth to some extent. You can’t get around bismuth completely but you can play with the percentages and do all of your tests, thermal cycling, stringing. We have to be aware in the stringer, if we have 0.5% more breakage, this is too much. If we have below 0.1% this might be OK. It’s a balance to find how much stress to put on the cell, the cost for the alloy and whether the bonding is strong enough. But in the end we are pretty close to matching the cost and we have talked in the PV industry about replacing lead since the beginning. There are many different opinions.
The cost is still slightly above, you don’t get it completely for free yet. But it’s also a ‘math game’. If you spend the same focus on this that you spend on getting efficiency up or getting more Watts out you would fix it. It’s a question of focus. The PV industry is fighting a cost battle.
And it is bismuth that keeps the soldering temperature lower?
Not only, but bismuth helps to have a lower soldering temperature. And bismuth is interesting because it has already replaced around one third of lead soldering globally.
It’s a principle thing to look for new and alternative materials. It’s an ongoing process, we continue to do testing, we have a very nice mixture with copper or nickel which has worked well. Then it’s also a cost thing. If you really are free on the cost, you can find a new solution without bismuth. Then your product is likely more than 5% more expensive but that’s not something the market will accept. If you said this to a standard module maker or a volume provider in solar home systems they will tell you it’s not possible.
There might be other applications, for example in the smart city market, where we work now doing modules for parking meters or smart street lights. There might be certain parts where the module component is more flexible in design and cost.
This is something we have learned, being in the off-grid market. We are not perceived as the solar guys any more. We deliver components which typically only add up to a very small portion of the cost, and it has to perform a function for a certain application. It needs to perform under certain conditions but it’s not this Watt-peak race, we have other drivers we have to look at in our R&D and production control.
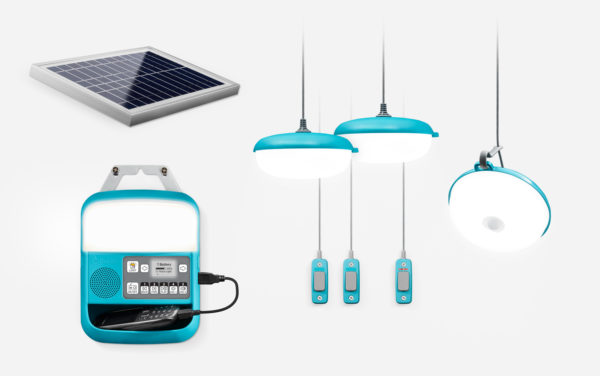
And do you see plenty more interest in lead-free modules among your customers?
We only recently made the announcement and launched the product with our customer Biolite. Now we are looking at feedback from the market and discussing this with different customers. It’s part of our discussions with customers anyway. Every year we have discussions on how we can improve, modify the bill of materials and design, bring costs down etc. And our customers are continuously developing new products.
So it’s not like the standard solar module industry, where it’s always the same module size. We have to be more flexible. If our customers add a larger TV to their solar home system offering, then instead of a 45 W module they will need 60 W, 80 W or even more. So we are continuously adjusting as our customers launch new product series.
And it’s the same for other customers in smart city applications. With a GPS tracker, the device can become a gateway for more functions and will need more power and the design will change. So we have these types of discussion as part of our regular business and lead-free soldering can be a part of this.
This is why off-grid module making is completely different from standard modules makers, in the whole mindset and the requirements.
What can you say on the warranty side with this module?
For the lead-free modules, we have a 20-year warranty and we expect they will last longer. We apply the same peeling force limit – 1.5 N/mm after [the] damp-heat test and thermo cycling test (TC), that the PV industry uses. We have tried how going down to 1 N/mm impacts the power loss after TC500, TC1000, and it might work for some applications but for now we stick with the 1.5 N/mm.
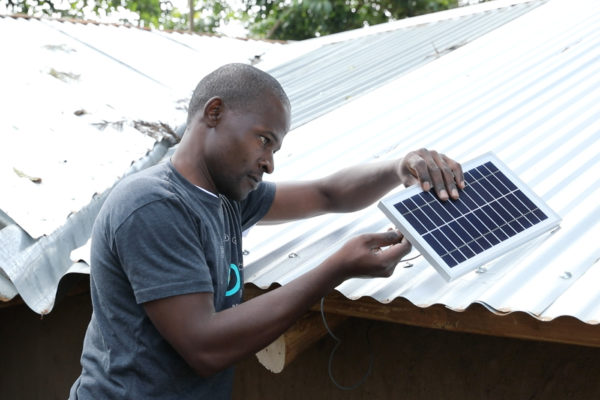
And how is the off-grid market looking for you at the moment?
The market is on the way up but consolidating a bit. For example Mobisol, a large player, has filed for insolvency [last] year but their business in Africa has been acquired and is moving forward with the French utility Engie. There have been very big growers and the end market is huge but its not a software model like Google or Facebook where you can scale very quickly. You have to get out to remote villages, install solar home systems. You have to collect your payments. Many of our customers are going through this phase right now.
As well as the energy access market, we have the smart city market and we see a lot of new applications coming up. We think from yearly installed solar modules only 1-2% are off-grid modules so this is not in the focus of the standard solar module industry.
This content is protected by copyright and may not be reused. If you want to cooperate with us and would like to reuse some of our content, please contact: editors@pv-magazine.com.
Sounds interesting