A group of researchers from the Fraunhofer Institute for Solar Energy Systems (ISE) in Germany has developed a new metallization technique for bifacial silicon heterojunction (SHJ) solar cells that they claim may considerably help reduce the amount of silver needed for their production while maintaining high levels of power conversion efficiency.
The scientists utilized rotary screen printing (RSP) for the front- and rear-side metallization of the bifacial SHJ solar cells via the “Rock-Star” demonstrator machine developed by the Fraunhofer ISE itself in partnership with German automation company ASYS Automatisierungssysteme GmbH.
This machine is able to achieve a cycle time of just 0.6 seconds per solar cell, which means a throughput increase by a factor of 1.5. It can also achieve a throughput of up to 8,000 wafers an hour in an inline configuration. “However, certain technical challenges must be overcome until these technologies can seriously challenge the predominance of FSP [flatbed screen printing] in the field of solar cell metallization,” the scientists stated.
The RSP unit is based on a mesh-based cylinder screen with a partly opened emulsion layer that serves as a printing form. During the printing process, the cylinder rotates and the paste is printed through the open areas of the rotating screen by a polyurethane (PU) squeegee within the screen. The wafer is transported through the printing unit on a carrier with vacuum fixation.
“The printing form is based on a fine stainless steel mesh which is enhanced with a thin, electroplated nickel layer in order to increase the stability of the mesh,” the research team stated. “Compared to fine meshes used for FSP screens, rotary screens need a considerably thicker wire thickness to enable a sufficient stability during the printing process.”
According to the researchers, the RSP technique was successfully carried out on the demonstrator machine at 50% percent of the maximum machine speed (0.86 s per cell) and 70% percent machine speed (0.65 s per cell). “In a virtual production line, these cycle times would correspond to a gross throughput of approximately 4100 (50% speed) and 5500 (70% speed) cells h−1 on a single track,” they emphasized.
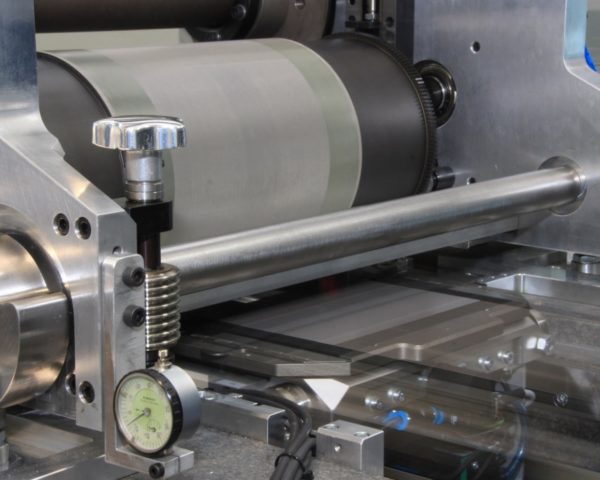
Image: Fraunhofer ISE
Through the proposed technique, the academics were able to produce a fully metallized bifacial silicon heterojunction solar cell with a power conversion efficiency of 21.7%, which compares to an efficiency of 22.1% of a reference cell built with FSP — currently the dominating technology for industrial metallization of crystalline silicon solar cells with a market share of over 98%.
“Using RSP for the front- and/or rear-side metallization reveals an impressive reduction of the average wet silver paste laydown by 60–70% (fully RSP printed cells) and 49% (RSP rear side, FSP front side) compared to the FSP reference process,” they further explained. “This corresponds to a very low total silver consumption of 6-9 mg W for bifacial solar cells fully or partly metallized with RSP compared to 17 mg W.”
The group presented its findings in the study “Rotary Screen Printed Metallization of Heterojunction Solar Cells: Toward High-Throughput Production with Very Low Silver Laydown,” published in Energy Technology.
This content is protected by copyright and may not be reused. If you want to cooperate with us and would like to reuse some of our content, please contact: editors@pv-magazine.com.
By submitting this form you agree to pv magazine using your data for the purposes of publishing your comment.
Your personal data will only be disclosed or otherwise transmitted to third parties for the purposes of spam filtering or if this is necessary for technical maintenance of the website. Any other transfer to third parties will not take place unless this is justified on the basis of applicable data protection regulations or if pv magazine is legally obliged to do so.
You may revoke this consent at any time with effect for the future, in which case your personal data will be deleted immediately. Otherwise, your data will be deleted if pv magazine has processed your request or the purpose of data storage is fulfilled.
Further information on data privacy can be found in our Data Protection Policy.