A group of researchers led by Germany’s Insititute for Solar Energy Research Hamelin (ISFH) have fabricated an n+-type polysilicon on oxide (POLO) back junction solar cell with a passivation layer stack based on aluminum oxide (AlOx) and silicon nitride (SiNy).
“Our study shows for the first time an effective industrial cleaning and passivation for undiffused textured front side with excellent passivation quality,” the research's lead author, Byungsul Min, told pv magazine. Especially, the AlOx/SiNy passivation layer stack is fabricated with an industrial plasma enhanced chemical vapor deposition (PECVD) system with a low-frequency (LF) plasma source which is much more cost-effective than atomic layer deposition (ALD) systems or PECVD systems with a high-frequency (HF) plasma source.”
The novel cell technology was introduced in the paper “24.2% efficient POLO back junction solar cell with an AlOx/SiNy dielectric stack from an industrial-scale direct plasma-enhanced chemical vapor deposition system,” published in Progress in Photovoltaics. “Our results show a path for the industrialization of novel cell concepts without diffusion at the front side like our POLO back junction solar cell, but it is also relevant for a mainstream concept such as TOPCon which uses mainly ALD system for their AlOx layer.”
The group built a 156.75 mm x 156.75 mm POLO cell with a gallium-doped Czochralski-grown silicon wafer with a resistivity of 0.73 Ωcm. To deposit the AlOx layer it utilized an industrial batch-type LF-PECVD system provided by German PV equipment manufacturer Centrotherm, whose researchers also contributed to the research. “We then adapt the recipe by varying the thickness of the silicon oxide (SiO2) layer beneath the AlOx layer between 0 and 2 nm, the thickness of the AlOx layer between 5 and 15 nm thicknesses, and the refractive index of the SiNy layer between 2.05 and 2.4,” the researchers explained.
They also built a reference device based on a textured gallium-doped Czochralski-grown wafer with a resistivity of 0.9 Ωcm that was passivated with a 10-nm-thick AlOx layer deposited by ALD and a SiN y layer. “After the screen-printing of the aluminum grid on the front and silver grid on the rear, the samples are co-fired in a belt furnace at the peak firing temperatures between 800 C and 810 C,” they further explained.
Tested under standard illumination conditions, the POLO cell achieved a power conversion efficiency of 24.2%, an open-circuit voltage of 725 mV, a short-circuit current density of 40.2 mA/cm2, and a fill factor of 83.0%, with the results being confirmed by ISFH CalTeC. The benchmark device achieved an efficiency of 24.1% an open-circuit voltage of 725 mV, a short-circuit density of 39.9 mA/cm2, and a fill factor of 83.2%.
“The integration of this passivation sequence into our current process flow for POLO BJ solar cells has been successfully demonstrated with POLO BJ solar cells, which show even higher cell efficiencies than the reference fabricated with lab-scale processes,” the researchers concluded.
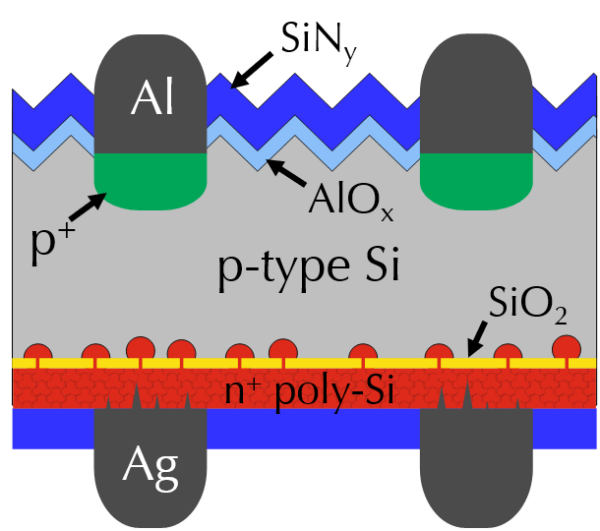
Image: Insititute for Solar Energy Research Hamelin (ISFH)
This content is protected by copyright and may not be reused. If you want to cooperate with us and would like to reuse some of our content, please contact: editors@pv-magazine.com.
By submitting this form you agree to pv magazine using your data for the purposes of publishing your comment.
Your personal data will only be disclosed or otherwise transmitted to third parties for the purposes of spam filtering or if this is necessary for technical maintenance of the website. Any other transfer to third parties will not take place unless this is justified on the basis of applicable data protection regulations or if pv magazine is legally obliged to do so.
You may revoke this consent at any time with effect for the future, in which case your personal data will be deleted immediately. Otherwise, your data will be deleted if pv magazine has processed your request or the purpose of data storage is fulfilled.
Further information on data privacy can be found in our Data Protection Policy.