Swedish company Sticky Solar Power says it is ready to move into a new phase of pilot production for its ‘tape solution’ cell interconnection method. Sticky Solar said the process has several advantages over current module manufacturing soldering approaches and should also compare favorably with Meyer Burger’s SmartWire solution.
The high temperatures involved in the soldering used in standard module production mean the approach is unsuitable for high efficiency cell concepts such as heterojunction (HJT) products. With a shift toward roundwires and multibusbar (MBB) technologies raising further cell interconnection concerns, manufacturers, as ever, are waiting on a low-cost process which can deliver high throughput.
Sticky Solar’s Tape Solution does away with soldering entirely by instead placing a sticky tape around the interconnection ribbon which holds the wire in place through the ensuing manufacturing stages. A firm connection is then created by the heat and pressure applied to the module during lamination.
The highly transparent tape reportedly offers very strong ultraviolet (UV) resistance.
“Our process allows us to offer significantly reduced capex [capital expenditure] and perceived risk,” said Sticky Solar joint chief executive Beatriz Roza. “These are significant benefits in the current market.”
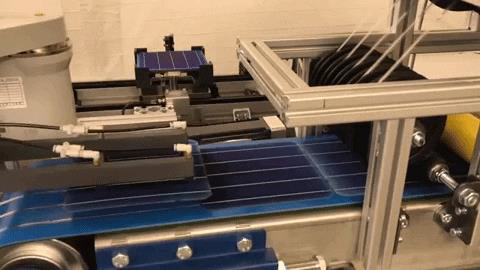
Image: Sticky Solar Power
The company was not prepared to reveal throughput figures but said it could be greatly increased with the tape approach.
“We roll out the tape in a continuous motion,” said fellow CEO Jonas Buddgård. “A robot places the cells on the fly, there is no starting and stopping as with soldering. The bottleneck in terms of cycle time is the robot, and we can increase the number of robot arms.”
By eliminating solder, the process can also reduce the amount of silver required while addressing the issue of exposure to high temperatures in HJT and other high-efficiency-cell production. The process has only been tested with a flat ribbon thus far but there are plans to test with round wire and having it held in place by tape could offer a solution to keeping such materials aligned.
Pilot
Sticky Solar said it has had strong interest from manufacturers and is ready to move into pilot production. The company said it wants to work closely with customers to iron out issues which may not have been obvious at the R&D phase. Sticky Solar has applied for EU funding for the pilot production phase and plans to begin searching for manufacturers to join its project this year.
“The next two or three years will be very interesting in terms of the establishment of manufacturing in Europe, the window is definitely there for novel process improvements,” said Buddgård. “We hope to participate in the various solar manufacturing initiatives, not least because this might open up some early contacts with these manufacturing projects.”
This content is protected by copyright and may not be reused. If you want to cooperate with us and would like to reuse some of our content, please contact: editors@pv-magazine.com.
Four words that I like to see in one sentence when it comes to technological innovation “low cost” and “high performance”.
Especially in this very important subject that is solar energy, the more the system evolves, the more advisable it becomes. I hope you will reach a favorable conclusion in the next steps of this project. Congratulations Pv Magazine for keeping us informed on this very important matter.