Researchers from the AGH University of Science and Technology in Poland have constructed a micro compressed air energy storage (CAES) system based on a reciprocating drive air expander.
The novel solution is intended for use in residential and industrial applications requiring additional low-temperature waste heat and intermittent control strategies. “This system is currently a prototype but we are now constructing a more efficient version,” the research's corresponding author, Jacek S. Leszczynski, told pv magazine.
The system consists of a compressor, a piston, a piston rod, a connecting rod, a mechanical crank, and a crankshaft. It also utilizes a thermal energy storage (TES) unit to improve the controllability of the compressed air expansion process performance via pulse width modulation (PWM). The latter is a method that is commonly utilized to control analog devices, using a digital signal.
The storage section of the system comprises an isobaric tank that stores compressed air in the form of mechanical energy and the TES unit, which stores the heat generated during compression. A pulse heat exchanger controlled by PWM is used to heat the compressed air portions and a system of flow control valves. The mechanical crank system is then linked via a gear to an electrical power generator.
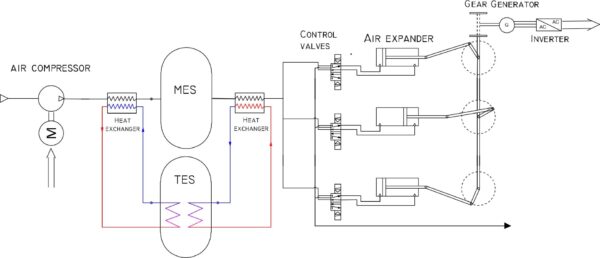
Image: AGH University of Science and Technology
“The expansion section includes drive elements in the form of actuators that convert the mechanical energy of the compressed air into mechanical energy of the reciprocating motion of the piston and piston rod,” the scientists explained. “This section expands the compressed air into the atmosphere after work in the actuator chamber.”
The academics conducted an analysis of the system performance with a multiple drive with the aim of assessing its effects on the air expander operation. “It was decided to present a comparison of the air expander dynamics consisting of one, three, five and seven linear drives, for which the sum of piston diameter is equal in each case,” they specified, adding that the analysis considered generated power, shaft rotational speed, air consumption, and volume flows.
The test showed that the multi-drive system not only raises the unit’s efficiency but also stabilizes the rotational speed, which in turn increases the generated electrical power. “The three-drive expander had the highest electrical power compared to the five- and seven-drive expanders, and much lower electrical power fluctuation than the single-drive expander,” they also noted.
The researchers also found that the system's optimal duty cycle of air-supplied PWM control is 0.5, which results in an electrical power of 1.1 kW and energy efficiency of 65% for the air expander.
This duty cycle, in their view, has the ability to control the electric power while maintaining an acceptable overall efficiency value. “In the analyzed case, the range of electric power variability was 500–1800 W, i.e. from 20 to 75% of maximum power with a change in overall efficiency from 90 to 100% of the maximum efficiency,” they said.
The system was presented in the study “Analysis of optimal expansion dynamics in a reciprocating drive for a micro-CAES production system,” published in Applied Energy.
This content is protected by copyright and may not be reused. If you want to cooperate with us and would like to reuse some of our content, please contact: editors@pv-magazine.com.
By submitting this form you agree to pv magazine using your data for the purposes of publishing your comment.
Your personal data will only be disclosed or otherwise transmitted to third parties for the purposes of spam filtering or if this is necessary for technical maintenance of the website. Any other transfer to third parties will not take place unless this is justified on the basis of applicable data protection regulations or if pv magazine is legally obliged to do so.
You may revoke this consent at any time with effect for the future, in which case your personal data will be deleted immediately. Otherwise, your data will be deleted if pv magazine has processed your request or the purpose of data storage is fulfilled.
Further information on data privacy can be found in our Data Protection Policy.